مبانی جمعیت شناسی pdf بارگیری رایگان کتاب مبانی جمعیت شناسی سعید تمنا ، مبانی جمعیت شناسی کتاب راهنمای بایامی نور
دانشجویان و کاربران گرامی ، محتوای این فایل خلاصه مبانی جمعیت شناسی سعید تیمنا (تا فصل هشتم) در فرم پاورپوینت قابل ویرایش نیست در 156 اسلاید با فلش کارت ها و نکات مهم این دوره و همچنین بانک نمونه سوالات دوره های قبلی دانشگاه پیام نور با پاسخ ، تهیه شده و با بهترین کیفیت توسط تیم وب سایت ما تهیه و تدوین شده است.
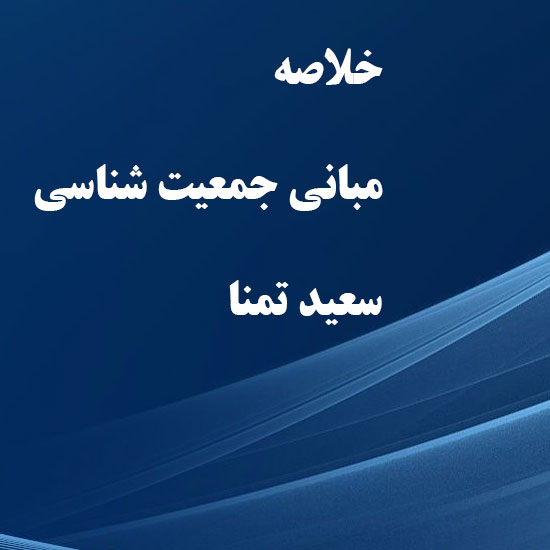
فهرست فصول کتاب ضروریات جمعیت شناسی سعید تیمنا:
فصل اول:
کلیات و مفاهیم
فصل دوم:
ماهیت و انواع روشهای تحقیق در جمعیت شناسی
فصل سوم:
توزیع جغرافیایی جمعیت
فصل چهارم:
ترکیب سن و جنس جمعیت
فصل پنجم:
جمعیت شناسی از نظر فعالیت و اشتغال
فصل ششم:
جمعیت شناسی از نظر موقعیت اجتماعی و خانوادگی
فصل 7:
جمعیت شناسی از نظر تحصیلات و سواد
فصل 8:
جمعیت ، بهداشت و مسکن
مبانی سوالات جمعیت شناسی با پاسخنامه دانشگاه پیام نور که شامل ترم های زیر است:
سوالات ترم اول 99-98 با پاسخ
نمونه سوالات تابستان 98 به همراه پاسخنامه
سوالات نیمسال دوم 98-97 نیمسال دوم همراه با پاسخ
سوالات نیمسال اول 98-97 همراه با پاسخ
سوالات نیمسال دوم 97-96 به همراه پاسخنامه
سوالات نیمسال اول 97-96 با پاسخ
نمونه 96 سوال همراه با پاسخ
سوالات نیمسال دوم 96-95 همراه با پاسخ
نیمسال اول 96-95 سوالات همراه با پاسخ
سوالات نیمسال دوم 95-94 به همراه پاسخنامه
نیمسال اول 95-94 سوالات همراه با پاسخ
نمونه سوالات تابستان 94 همراه با پاسخ
سوالات نیمسال دوم 94-93 با پاسخ
سوالات نیمسال اول 94-93 با پاسخ
نمونه 93 سوال تابستانی همراه با پاسخ
سوالات نیمسال دوم 93-92 با پاسخ
سوالات نیمسال اول 93-92 با پاسخ
نمونه 92 سوال تابستانی همراه با پاسخ
سوالات نیمسال دوم 92-91 به همراه پاسخنامه
سوالات نیمسال اول 92-91 به همراه پاسخنامه
نمونه 91 سوال تابستانی همراه با پاسخ
سوالات نیمسال دوم 91-90 همراه با پاسخ
نیمسال اول 91-90 س questionsال همراه با پاسخ
نمونه تابستانی 90 سوال با پاسخ
سوالات نیمسال دوم 90-89 همراه با پاسخ
نیمسال اول 90-89 سوالات با پاسخ
نمونه سوالات تابستانی 89 با پاسخ
سوالات نیمسال دوم 89-88 با پاسخ
سوالات نیمسال اول 89-88 با پاسخ
سوالات نیمسال دوم 88-87 همراه با پاسخ
سوالات نیمسال اول 88-87 همراه با پاسخ
نکات مهم: پس از پرداخت ، لینک دانلود به شما نشان داده می شود و برای تأیید بیشتر ، یک لینک بارگیری دیگر به ایمیل شما ارسال می شود.
نکته: ما پیشنهاد می کنیمخلاصه کتاب “اندازه گیری در علوم شمشیر آموزشی”در وب سایت فایل پدیده.
نوع فایل: ppt